Новая диагностическая система стартовала на ДГОКе
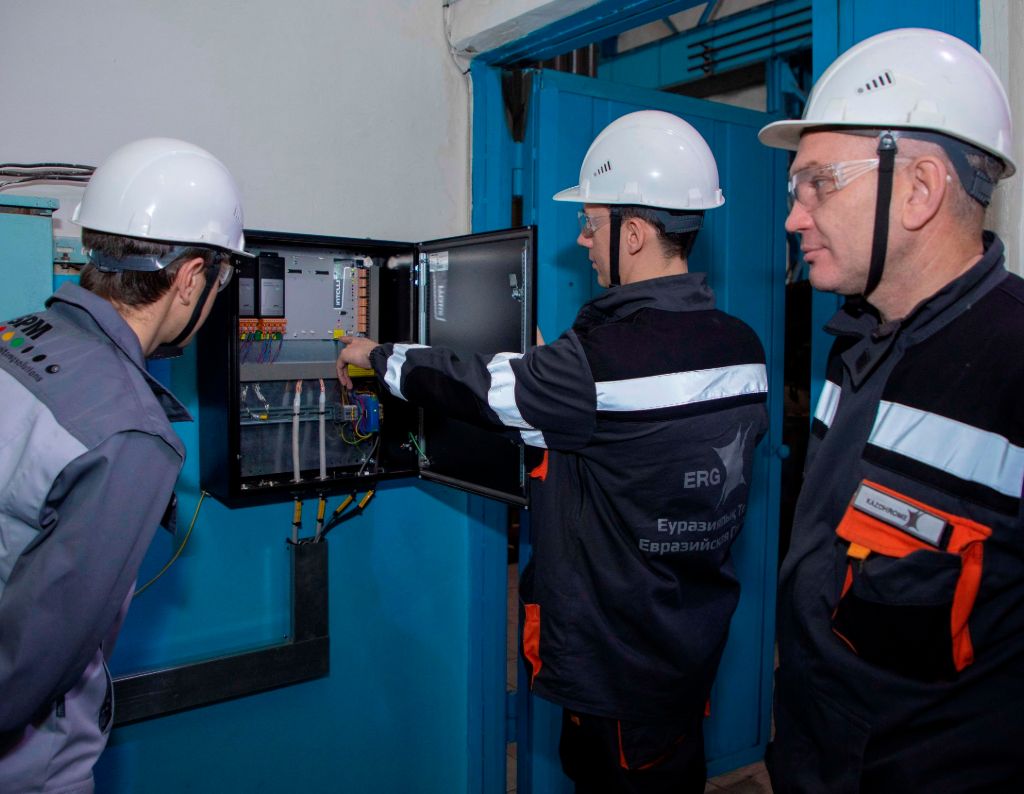
Больше надежности, меньше простоев — в «Казхроме» стартовала система стационарной диагностики оборудования. Пилотной площадкой для новшества стал Донской ГОК. Внедрена система в двух крупных цехах — на шахте «Десять лет независимости Казахстана» и фабрике обогащения и окомкования руды.
Красный, желтый, зеленый
Те узлы, работу которых не видно невооруженным глазом, теперь отображаются на мониторах, а их состояние легко отследить в онлайн режиме. Подшипниковые узлы ряда оборудования на шахте «Десять лет независимости Казахстана» и фабрике обогащения и окомкования руды оснастили датчиками, которые позволят в реальном времени контролировать их работу. Всего установлено 200 точек измерения на 16 единицах оборудования. Монтаж оборудования, пусконаладку и запуск выполнила российская компания «СПМ-Инструмент».
‒ Система нужна для мониторинга оборудования и его диагностики, ‒ рассказывает менеджер по технической диагностике и мониторингу АО «ТНК «Казхром» Глеб Шевченко. ‒ На оборудовании в реальном времени контролируются подшипниковые узлы. С помощью программных алгоритмов показания обрабатываются, выдается заключение по состоянию подшипников узлов оборудования ‒ двигателя, редуктора, привода.
Принципы работы датчиков — измерение параметров вибрации, в том числе методом ударных импульсов, для контроля общего состояния и выявления дефектов в подшипниках качения. Измерение производится с определенным промежутком времени ‒ так, на агрегатах жизнеобеспечения, к которым относятся главная вентиляторная установка шахты и подъемные машины, это каждые три минуты.
‒ На шахтном оборудовании по три датчика на одном подшипнике, ‒ говорит инженер технической поддержки ООО «СПМ Инструмент» Юрий Слесаренко. ‒ Контроль производится в трех направлениях ‒ вертикальном, горизонтальном и осевом.
Сигналы, поступающие на мониторы операторов, отображены по принципу светофора: зеленый цвет ‒ нормальная работа, желтый ‒ предупреждение. Критического красного уровня можно избежать. На примере работы подшипниковых узлов привода вентиляторной установки шахты видно: все узлы работают в стабильном нормальном режиме. Журнал оперативных тревог ‒ пуст.
‒ Визуально подшипники закрыты, но теперь мы знаем об их состоянии все, ‒ говорит моторист вентиляторной установки шахты «Десять лет независимости Казахстана» Раиса Чувильская. ‒ Если показания изменятся, я сообщу своему руководству, и мы успеем принять меры. Вибрация не должна выходить за определенные пределы в каждой из зон. Для «зеленой» зоны такой предел — 4,5 мм/сек.
‒ Заранее зная ситуацию, возможно устранить дефект до поломки, ‒ говорит начальник отдела по надежности оборудования Дмитрий Зинченко. ‒ Это снизит и затраты на ремонт, и устранит фактор внезапности. От внедрения системы ожидаем снижения количества внезапных аварийных ситуаций. Диагностам система позволит уйти от «полевых» работ — замеров, непосредственно, на самих агрегатах, и больше времени уделить анализу.
Минимизация отказов оборудования, внеплановых простоев, оптимизация затрат на ремонтные работы ‒ не единственные плюсы. Нововведение сократит и плановые простои за счет владения ситуацией, а значит, возможности заранее подготовить к ППР материалы, инструмент и ремонтный персонал.
Первыми сигналы системы видят сотрудники, которые работают с оборудованием постоянно. На фабрике обогащения и окомкования руды показания выводятся на мониторы операторов участков производства окатышей № 1 и 2 (УПО), а также и в диспетчерской корпуса среднего дробления.
Ковшовый конвейер «Aumond», шаровая мельница, барабанный окомкователь — на обоих УПО, конвейер № 2, щековая дробилка и пластинчатый питатель в корпусе крупного дробления — на участках фабрики стационарная система охватила наиболее ресурсоемкое в плане времени ремонта, а также нужных к нему материалов и запчастей, оборудование. Оно входит в основную технологическую цепочку производства окатышей, и от него зависит работа «сердца» фабрики — обжиговой печи.
Вся история измерений сохраняется, ее можно посмотреть за любой период времени. С ФООР такая информация передается по локальной сети в базу данных сервера диагностики, который находится в цехе автоматизации и связи. Это позволит специалистам контролировать и анализировать состояние оборудования удаленно.
В целом по компании взят курс на цифровизацию и оснащение оборудования системами прогнозной аналитики технического состояния. Так пилотные проекты внедряются в Актюбинском и Аксуском заводах ферросплавов. В перспективе развития полный охват всего наиболее критичного технологического оборудования Компании с созданием единого центра мониторинга.